Eliminating Controlled Obsolescence with Duravi: Driving Profitability and Sustainability
Eliminating Controlled Obsolescence with Duravi: Driving Profitability and Sustainability
Eliminating Controlled Obsolescence with Duravi: Driving Profitability and Sustainability
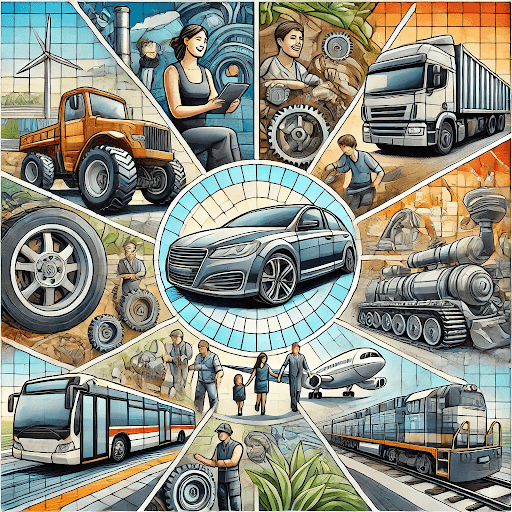
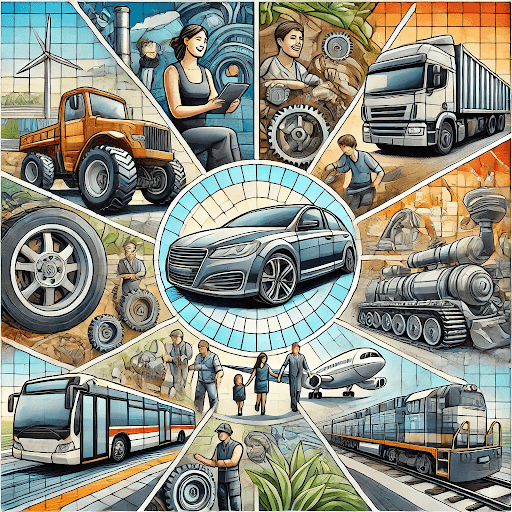
By Tommy W Denning Jr / President @ Duravi
Controlled obsolescence, a strategy where products are designed to have limited lifespans or become outdated quickly, has long been a bane for consumers and organizations alike. This business model, while profitable for manufacturers, often leads to higher costs for end-users and significant environmental impacts.
Duravi, with its revolutionary line of surface transmutation technology solutions, presents a compelling solution to these issues, enhancing product longevity and driving profitability for organizations by mitigating the effects of controlled obsolescence.
Understanding Controlled Obsolescence
Controlled obsolescence, also known as planned obsolescence, involves designing products with a predetermined lifespan. This strategy encourages frequent repurchases, boosting sales and ensuring continuous revenue streams for manufacturers. However, it comes at a cost:
Shortened Product Lifespan: Products are designed to fail or become obsolete after a specific period, leading to increased consumer spending. For example, mechanical parts in machinery and equipment may be made from materials that wear out quickly or are susceptible to rapid degradation under normal operating conditions. This intentional limitation ensures that the equipment will need to be replaced or extensively repaired more frequently than would be necessary with more durable components.
Perceived Obsolescence: Consumers are made to feel their current products are outdated due to regular release cycles of new models with minor upgrades or aesthetic changes. In manufacturing and industrial contexts, this might involve introducing slightly improved or cosmetically different versions of tools, machinery, or equipment, making existing models seem inferior or less efficient. This perceived need to upgrade, even when the older models are still functional, drives additional sales.
Non-Upgradeable Designs: Products are made difficult to upgrade, such as machinery with non-replaceable components or designs that prevent easy maintenance. For instance, industrial machines might be built with integral parts that cannot be individually replaced or repaired, forcing the entire unit to be discarded and replaced. This lack of upgradeability or modularity increases waste and costs, as companies must invest in entirely new equipment rather than simply upgrading existing systems.
Economic and Environmental Impact: This model drives economic growth but leads to higher consumer costs and increased waste, particularly from discarded mechanical parts and materials. The frequent need for replacements contributes to significant resource consumption and environmental degradation. For example, the manufacturing and disposal of machinery components generate substantial waste and emissions, exacerbating environmental issues. Additionally, increased corrosion and wear due to inferior materials not only shorten product life but also lead to higher maintenance costs and downtime, further straining financial and environmental resources.
By focusing on mechanical, manufacturing, and corrosion protection aspects, controlled obsolescence highlights the recurring need for maintenance and replacements in industrial applications. This approach drives up costs, increases resource consumption, and impacts sustainability, creating challenges for both consumers and the environment.
Duravi’s Technological Edge
Duravi’s core technology addresses the addressable issues of controlled obsolescence through its innovative approach to friction and wear reduction. The Duravi process involves a transmutation at the micro- and molecular level that nearly eliminates friction in contacting surfaces.
Here’s how Duravi's technology stands out:
Friction Reduction and Wear Resistance:
Duravi's transmutation process decreases friction by up to 90% through the “smoothing” of contacting surfaces at a microscopic level and “armoring” the underlying molecular structures without compromising – often enhancing – the material characteristics. This process not only creates a near-frictionless outer layer but also significantly enhances the wear resistance of metal surfaces. As a result, components treated with Duravi experience dramatically longer lifespans and reduced need for frequent replacements, ensuring sustained performance and reliability.
Surface Conditioning:
Duravi improves the tribological properties of materials, embedding within the surfaces to reduce friction, reduce corrosion/oxidation, and prevent lubricant breakdown. This not only extends the life cycle of traditional lubricant regimes but, offers enhanced protection against the complete or catastrophic failure of such products. By making the contacting surfaces “semi-inherently frictionless” Duravi additives dramatically increase the usable life of your “off-the-shelf” solutions and adds to the response time of failing lubricant regimes by adding a layer of protection at the surface and molecular levels.
Vibration Reduction:
Duravi’s technology reduces vibration in mechanical systems, which is a key factor in extending the longevity of equipment. Less vibration means lower mechanical stress and fatigue on components, resulting in fewer breakdowns and longer service intervals. Duravi systems just operate more smoothly – this leads to less overall mechanical stress and an enhanced ability to catch or pre-diagnose system failures that may have been masked by excessive vibration and noise.
Corrosion Prevention:
General corrosion prevention through Duravi’s products adds immense value to both industry and consumers by maintaining the integrity of surfaces in harsh environments. The micro-smoothing action of Duravi technologies virtually eliminates the vectors for chemical and environmental oxidation inputs – from salt water and biologicals to general oxidation Duravi stops it all. This reduces maintenance costs, prevents unexpected failures, prolongs the operational life, and preserves the general appearance of equipment.
Compatibility and Sustainability:
Composed of 99% bio-based, non-toxic materials, all Duravi products are sustainably sourced and cruelty free.
Impact on Profitability and Sustainability
Eliminating the Need for Frequent Replacements: By drastically reducing friction and wear, Duravi products extend the lifespan of machinery and equipment, which means less frequent need for replacements. This reduction in controlled obsolescence leads to significant cost savings for organizations, as they can avoid the continual cycle of purchasing new products.
Enhancing Machinery Performance and Efficiency: Duravi products increase load capacity, reduce operating temperatures, and minimize weight loss during operation. This results in enhanced overall performance and longevity of machinery, leading to higher operational efficiency and reduced downtime.
Energy Savings and Reduced Emissions: The superior lubrication properties of Duravi products lead to reduced energy consumption and lower CO2 emissions. For example, applying Duravi lubricants in motors and engines has been shown to reduce energy consumption by up to 25% and carbon emissions by up to 40%.
Case Studies and Real-World Applications: Numerous case studies demonstrate the effectiveness of Duravi products. In industries such as shipping, aeronautics, agriculture, and mining, companies have reported millions in savings from reduced maintenance costs, extended equipment life, and improved efficiency.
Conclusion
Duravi's advanced bio-lubricant technology offers a transformative solution to the challenges posed by controlled obsolescence. By extending the life of products, reducing maintenance costs, and enhancing performance, Duravi not only drives profitability for organizations but also promotes sustainability. Reducing waste through the use of durable, efficient lubricants directly contributes to lowering pollution and conserving resources. With Duravi, organizations can achieve their sustainability objectives while simultaneously driving profitability and operational efficiency. Embracing such innovative solutions is a critical step towards a more sustainable and economically viable future, where the detrimental effects of controlled obsolescence are mitigated, and environmental stewardship becomes a reality. By addressing these issues head-on, Duravi products are paving the way for a future where equipment lasts longer, costs are reduced, and the environmental footprint is minimized, aligning with global environmental goals and initiatives.
By Tommy W Denning Jr / President @ Duravi
Controlled obsolescence, a strategy where products are designed to have limited lifespans or become outdated quickly, has long been a bane for consumers and organizations alike. This business model, while profitable for manufacturers, often leads to higher costs for end-users and significant environmental impacts.
Duravi, with its revolutionary line of surface transmutation technology solutions, presents a compelling solution to these issues, enhancing product longevity and driving profitability for organizations by mitigating the effects of controlled obsolescence.
Understanding Controlled Obsolescence
Controlled obsolescence, also known as planned obsolescence, involves designing products with a predetermined lifespan. This strategy encourages frequent repurchases, boosting sales and ensuring continuous revenue streams for manufacturers. However, it comes at a cost:
Shortened Product Lifespan: Products are designed to fail or become obsolete after a specific period, leading to increased consumer spending. For example, mechanical parts in machinery and equipment may be made from materials that wear out quickly or are susceptible to rapid degradation under normal operating conditions. This intentional limitation ensures that the equipment will need to be replaced or extensively repaired more frequently than would be necessary with more durable components.
Perceived Obsolescence: Consumers are made to feel their current products are outdated due to regular release cycles of new models with minor upgrades or aesthetic changes. In manufacturing and industrial contexts, this might involve introducing slightly improved or cosmetically different versions of tools, machinery, or equipment, making existing models seem inferior or less efficient. This perceived need to upgrade, even when the older models are still functional, drives additional sales.
Non-Upgradeable Designs: Products are made difficult to upgrade, such as machinery with non-replaceable components or designs that prevent easy maintenance. For instance, industrial machines might be built with integral parts that cannot be individually replaced or repaired, forcing the entire unit to be discarded and replaced. This lack of upgradeability or modularity increases waste and costs, as companies must invest in entirely new equipment rather than simply upgrading existing systems.
Economic and Environmental Impact: This model drives economic growth but leads to higher consumer costs and increased waste, particularly from discarded mechanical parts and materials. The frequent need for replacements contributes to significant resource consumption and environmental degradation. For example, the manufacturing and disposal of machinery components generate substantial waste and emissions, exacerbating environmental issues. Additionally, increased corrosion and wear due to inferior materials not only shorten product life but also lead to higher maintenance costs and downtime, further straining financial and environmental resources.
By focusing on mechanical, manufacturing, and corrosion protection aspects, controlled obsolescence highlights the recurring need for maintenance and replacements in industrial applications. This approach drives up costs, increases resource consumption, and impacts sustainability, creating challenges for both consumers and the environment.
Duravi’s Technological Edge
Duravi’s core technology addresses the addressable issues of controlled obsolescence through its innovative approach to friction and wear reduction. The Duravi process involves a transmutation at the micro- and molecular level that nearly eliminates friction in contacting surfaces.
Here’s how Duravi's technology stands out:
Friction Reduction and Wear Resistance:
Duravi's transmutation process decreases friction by up to 90% through the “smoothing” of contacting surfaces at a microscopic level and “armoring” the underlying molecular structures without compromising – often enhancing – the material characteristics. This process not only creates a near-frictionless outer layer but also significantly enhances the wear resistance of metal surfaces. As a result, components treated with Duravi experience dramatically longer lifespans and reduced need for frequent replacements, ensuring sustained performance and reliability.
Surface Conditioning:
Duravi improves the tribological properties of materials, embedding within the surfaces to reduce friction, reduce corrosion/oxidation, and prevent lubricant breakdown. This not only extends the life cycle of traditional lubricant regimes but, offers enhanced protection against the complete or catastrophic failure of such products. By making the contacting surfaces “semi-inherently frictionless” Duravi additives dramatically increase the usable life of your “off-the-shelf” solutions and adds to the response time of failing lubricant regimes by adding a layer of protection at the surface and molecular levels.
Vibration Reduction:
Duravi’s technology reduces vibration in mechanical systems, which is a key factor in extending the longevity of equipment. Less vibration means lower mechanical stress and fatigue on components, resulting in fewer breakdowns and longer service intervals. Duravi systems just operate more smoothly – this leads to less overall mechanical stress and an enhanced ability to catch or pre-diagnose system failures that may have been masked by excessive vibration and noise.
Corrosion Prevention:
General corrosion prevention through Duravi’s products adds immense value to both industry and consumers by maintaining the integrity of surfaces in harsh environments. The micro-smoothing action of Duravi technologies virtually eliminates the vectors for chemical and environmental oxidation inputs – from salt water and biologicals to general oxidation Duravi stops it all. This reduces maintenance costs, prevents unexpected failures, prolongs the operational life, and preserves the general appearance of equipment.
Compatibility and Sustainability:
Composed of 99% bio-based, non-toxic materials, all Duravi products are sustainably sourced and cruelty free.
Impact on Profitability and Sustainability
Eliminating the Need for Frequent Replacements: By drastically reducing friction and wear, Duravi products extend the lifespan of machinery and equipment, which means less frequent need for replacements. This reduction in controlled obsolescence leads to significant cost savings for organizations, as they can avoid the continual cycle of purchasing new products.
Enhancing Machinery Performance and Efficiency: Duravi products increase load capacity, reduce operating temperatures, and minimize weight loss during operation. This results in enhanced overall performance and longevity of machinery, leading to higher operational efficiency and reduced downtime.
Energy Savings and Reduced Emissions: The superior lubrication properties of Duravi products lead to reduced energy consumption and lower CO2 emissions. For example, applying Duravi lubricants in motors and engines has been shown to reduce energy consumption by up to 25% and carbon emissions by up to 40%.
Case Studies and Real-World Applications: Numerous case studies demonstrate the effectiveness of Duravi products. In industries such as shipping, aeronautics, agriculture, and mining, companies have reported millions in savings from reduced maintenance costs, extended equipment life, and improved efficiency.
Conclusion
Duravi's advanced bio-lubricant technology offers a transformative solution to the challenges posed by controlled obsolescence. By extending the life of products, reducing maintenance costs, and enhancing performance, Duravi not only drives profitability for organizations but also promotes sustainability. Reducing waste through the use of durable, efficient lubricants directly contributes to lowering pollution and conserving resources. With Duravi, organizations can achieve their sustainability objectives while simultaneously driving profitability and operational efficiency. Embracing such innovative solutions is a critical step towards a more sustainable and economically viable future, where the detrimental effects of controlled obsolescence are mitigated, and environmental stewardship becomes a reality. By addressing these issues head-on, Duravi products are paving the way for a future where equipment lasts longer, costs are reduced, and the environmental footprint is minimized, aligning with global environmental goals and initiatives.
By Tommy W Denning Jr / President @ Duravi
Controlled obsolescence, a strategy where products are designed to have limited lifespans or become outdated quickly, has long been a bane for consumers and organizations alike. This business model, while profitable for manufacturers, often leads to higher costs for end-users and significant environmental impacts.
Duravi, with its revolutionary line of surface transmutation technology solutions, presents a compelling solution to these issues, enhancing product longevity and driving profitability for organizations by mitigating the effects of controlled obsolescence.
Understanding Controlled Obsolescence
Controlled obsolescence, also known as planned obsolescence, involves designing products with a predetermined lifespan. This strategy encourages frequent repurchases, boosting sales and ensuring continuous revenue streams for manufacturers. However, it comes at a cost:
Shortened Product Lifespan: Products are designed to fail or become obsolete after a specific period, leading to increased consumer spending. For example, mechanical parts in machinery and equipment may be made from materials that wear out quickly or are susceptible to rapid degradation under normal operating conditions. This intentional limitation ensures that the equipment will need to be replaced or extensively repaired more frequently than would be necessary with more durable components.
Perceived Obsolescence: Consumers are made to feel their current products are outdated due to regular release cycles of new models with minor upgrades or aesthetic changes. In manufacturing and industrial contexts, this might involve introducing slightly improved or cosmetically different versions of tools, machinery, or equipment, making existing models seem inferior or less efficient. This perceived need to upgrade, even when the older models are still functional, drives additional sales.
Non-Upgradeable Designs: Products are made difficult to upgrade, such as machinery with non-replaceable components or designs that prevent easy maintenance. For instance, industrial machines might be built with integral parts that cannot be individually replaced or repaired, forcing the entire unit to be discarded and replaced. This lack of upgradeability or modularity increases waste and costs, as companies must invest in entirely new equipment rather than simply upgrading existing systems.
Economic and Environmental Impact: This model drives economic growth but leads to higher consumer costs and increased waste, particularly from discarded mechanical parts and materials. The frequent need for replacements contributes to significant resource consumption and environmental degradation. For example, the manufacturing and disposal of machinery components generate substantial waste and emissions, exacerbating environmental issues. Additionally, increased corrosion and wear due to inferior materials not only shorten product life but also lead to higher maintenance costs and downtime, further straining financial and environmental resources.
By focusing on mechanical, manufacturing, and corrosion protection aspects, controlled obsolescence highlights the recurring need for maintenance and replacements in industrial applications. This approach drives up costs, increases resource consumption, and impacts sustainability, creating challenges for both consumers and the environment.
Duravi’s Technological Edge
Duravi’s core technology addresses the addressable issues of controlled obsolescence through its innovative approach to friction and wear reduction. The Duravi process involves a transmutation at the micro- and molecular level that nearly eliminates friction in contacting surfaces.
Here’s how Duravi's technology stands out:
Friction Reduction and Wear Resistance:
Duravi's transmutation process decreases friction by up to 90% through the “smoothing” of contacting surfaces at a microscopic level and “armoring” the underlying molecular structures without compromising – often enhancing – the material characteristics. This process not only creates a near-frictionless outer layer but also significantly enhances the wear resistance of metal surfaces. As a result, components treated with Duravi experience dramatically longer lifespans and reduced need for frequent replacements, ensuring sustained performance and reliability.
Surface Conditioning:
Duravi improves the tribological properties of materials, embedding within the surfaces to reduce friction, reduce corrosion/oxidation, and prevent lubricant breakdown. This not only extends the life cycle of traditional lubricant regimes but, offers enhanced protection against the complete or catastrophic failure of such products. By making the contacting surfaces “semi-inherently frictionless” Duravi additives dramatically increase the usable life of your “off-the-shelf” solutions and adds to the response time of failing lubricant regimes by adding a layer of protection at the surface and molecular levels.
Vibration Reduction:
Duravi’s technology reduces vibration in mechanical systems, which is a key factor in extending the longevity of equipment. Less vibration means lower mechanical stress and fatigue on components, resulting in fewer breakdowns and longer service intervals. Duravi systems just operate more smoothly – this leads to less overall mechanical stress and an enhanced ability to catch or pre-diagnose system failures that may have been masked by excessive vibration and noise.
Corrosion Prevention:
General corrosion prevention through Duravi’s products adds immense value to both industry and consumers by maintaining the integrity of surfaces in harsh environments. The micro-smoothing action of Duravi technologies virtually eliminates the vectors for chemical and environmental oxidation inputs – from salt water and biologicals to general oxidation Duravi stops it all. This reduces maintenance costs, prevents unexpected failures, prolongs the operational life, and preserves the general appearance of equipment.
Compatibility and Sustainability:
Composed of 99% bio-based, non-toxic materials, all Duravi products are sustainably sourced and cruelty free.
Impact on Profitability and Sustainability
Eliminating the Need for Frequent Replacements: By drastically reducing friction and wear, Duravi products extend the lifespan of machinery and equipment, which means less frequent need for replacements. This reduction in controlled obsolescence leads to significant cost savings for organizations, as they can avoid the continual cycle of purchasing new products.
Enhancing Machinery Performance and Efficiency: Duravi products increase load capacity, reduce operating temperatures, and minimize weight loss during operation. This results in enhanced overall performance and longevity of machinery, leading to higher operational efficiency and reduced downtime.
Energy Savings and Reduced Emissions: The superior lubrication properties of Duravi products lead to reduced energy consumption and lower CO2 emissions. For example, applying Duravi lubricants in motors and engines has been shown to reduce energy consumption by up to 25% and carbon emissions by up to 40%.
Case Studies and Real-World Applications: Numerous case studies demonstrate the effectiveness of Duravi products. In industries such as shipping, aeronautics, agriculture, and mining, companies have reported millions in savings from reduced maintenance costs, extended equipment life, and improved efficiency.
Conclusion
Duravi's advanced bio-lubricant technology offers a transformative solution to the challenges posed by controlled obsolescence. By extending the life of products, reducing maintenance costs, and enhancing performance, Duravi not only drives profitability for organizations but also promotes sustainability. Reducing waste through the use of durable, efficient lubricants directly contributes to lowering pollution and conserving resources. With Duravi, organizations can achieve their sustainability objectives while simultaneously driving profitability and operational efficiency. Embracing such innovative solutions is a critical step towards a more sustainable and economically viable future, where the detrimental effects of controlled obsolescence are mitigated, and environmental stewardship becomes a reality. By addressing these issues head-on, Duravi products are paving the way for a future where equipment lasts longer, costs are reduced, and the environmental footprint is minimized, aligning with global environmental goals and initiatives.